Designing and building aquatic environments is a matter of balancing aesthetics and function. Part of the challenge is deciding where to place mechanical equipment.
Pool equipment—with all the pipes, valves, conduits, and industrial-looking components—is not pleasing to the eye. Unless you’re fond of the appearance of machinery, equipment sets can be unsightly. It’s like the backstage in a theater, it’s where the show really happens, but also the part that should be hidden from view.
Equipment should also not be heard. The noise of pumps and other components can be as aesthetically invasive as an equipment set that’s left in plain view. It can become a source of frequent annoyance to homeowners and sometimes their neighbors. Even with variable speed pump technology that significantly reduces noise, outdoor living areas still need to be completely isolated sonically to reduce the auditory annoyance.
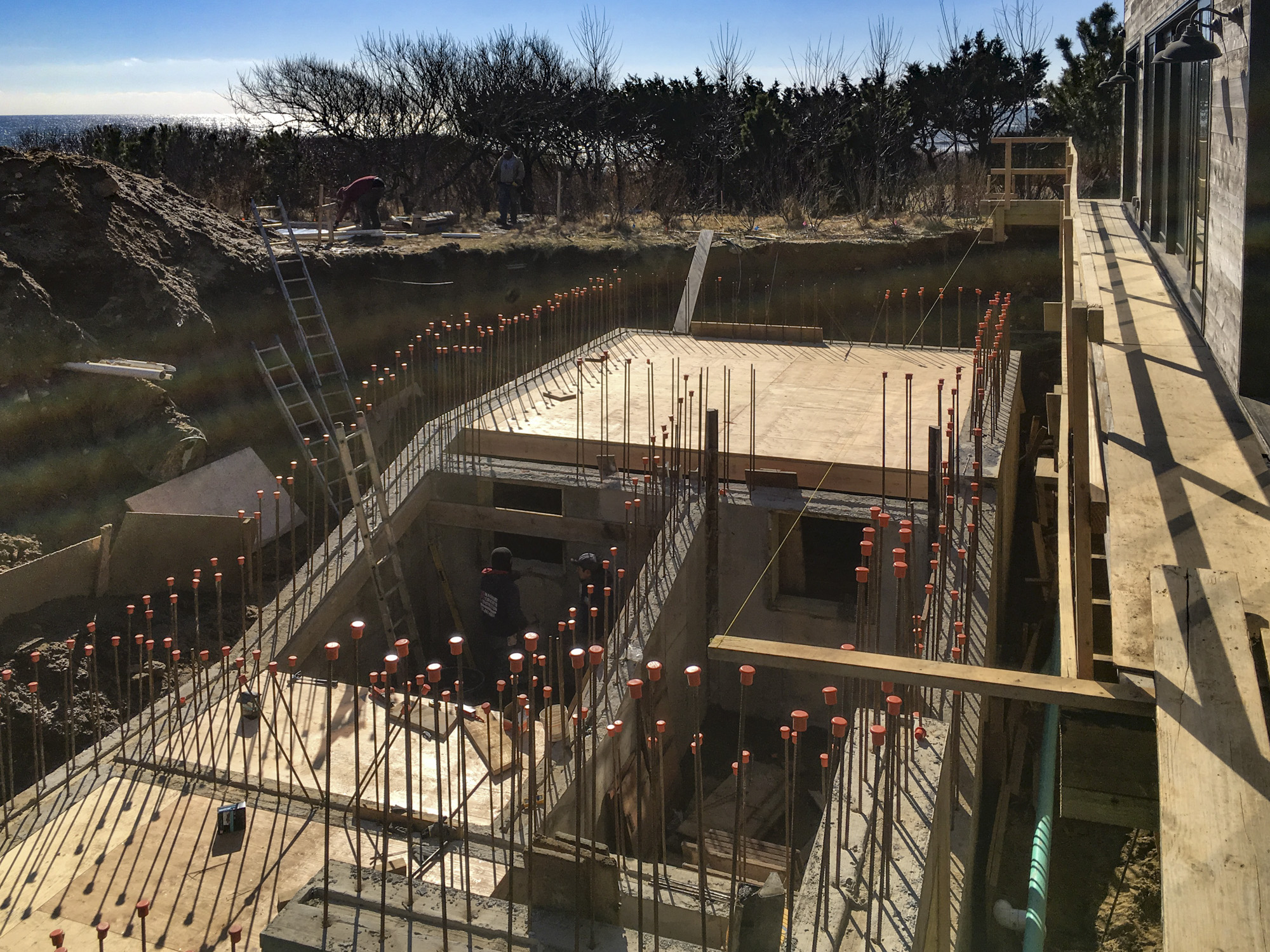

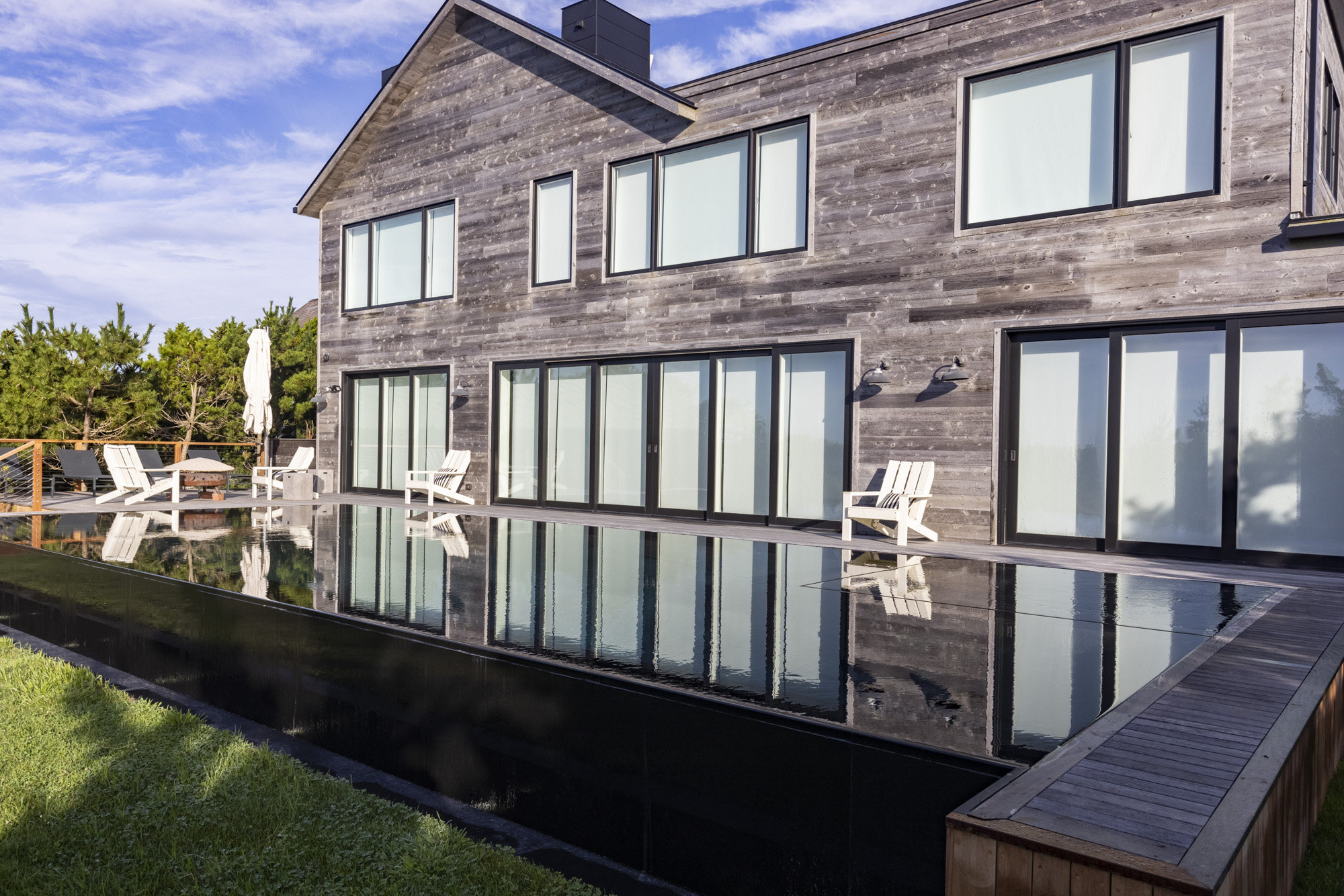
Major Problems: Sight, Sound and Space
Sight and sound are the two primary reasons why, whenever possible, I prefer to install equipment below grade in vaults—or as I like to call them, “bunkers.” Yes, it adds cost to the project, but the gains in noise elimination, visual harmony, and space use efficiency all add up to a wise investment for the homeowner.
But there’s more to it than just sight and sound. The value of real estate is another factor that pushes us and our clients in the downward direction. As housing prices increase and lot sizes shrink, there’s a growing need to make the most of all available space. If you calculate the cost per square foot of the area needed for a typical equipment set, especially one that’s spread out enough for convenient service and repair, the value of that square footage can be considerable.
Finding Space Below Ground
Added to that is the growing trend toward outdoor living. Many clients want to do more outside in terms of cooking, dining, and entertaining. That too can elevate the need to be as space efficient as possible. Again, going underground with the equipment is the perfect solution because it essentially expands the area you have available.
Finally, an equipment bunker provides the ultimate protection from the elements. The effects of weather, especially in our sometimes-harsh winters and searing hot summers, as well as the impact of UV degradation on equipment and plumbing, will almost inevitably extend the life of the equipment. Plus, everything stays clean which makes service easier, more pleasant, and far more manageable.
Vaults a.k.a “Bunkers”: A Wise Investment
There are, of course, different ways to go about locating an equipment bunker, which is largely dependent on the site specifics of the project at hand. Some builders opt for pre-manufactured, composite vaults that are installed somewhere adjacent to the pool below grade. There are hillside projects where cantilevered decks and pool structures can create spaces for locating equipment out of sight and out of mind.
When possible, we take the concept a step further and actually locate the bunker below the pool shell itself. As an example, we’re working on a project where we’re going down 25 feet below grade, building the bunker and a staircase for access, and then building the pool on top of the bunker. We’ve taken this approach before and it works. It gives us plenty of room to create a comfortable and accessible space, typically 10-by-20 feet with a 7-foot high ceiling.
We build our bunkers out of reinforced, poured-in-place concrete walls and floors and, of course, with heavily reinforced ceilings. The structures are always engineered and built for the soil conditions, which in this area, means building for freeze-thaw conditions. We install adequate drainage, in case of equipment leaks and sealed penetrations for plumbing and heater ventilation. We also properly ventilate the space itself, and we install proper lighting and watertight doors.
Accessing the “Bunker”
We’ve built vaults with ladders and hatches, but when we can, we prefer to install steps and doors. We want the equipment as accessible as possible so that homeowners and future servicers won’t hesitate to enter the space and spend time there servicing the system.
Yes, installing equipment in bunkers does add cost to the project, considerable cost, sometimes as much as $40,000. That number can dissuade some homeowners from the concept, but by the same token for many in the high-end, custom category, it takes little or no convincing. They don’t want to see or hear the equipment, and the additional advantage of saving space and protecting equipment also holds a strong appeal.
Certainly, bunkers aren’t for every project, but in the right situations, they offer an increased level of both enjoyment and product performance. That’s why going below ground enhances the experience that takes place above.